Ion Beam Milling Guide: Enhancing Surface Quality for High-Resolution Imaging and Analysis
Cross Sectioning and planar sample preparation for SEM and LM
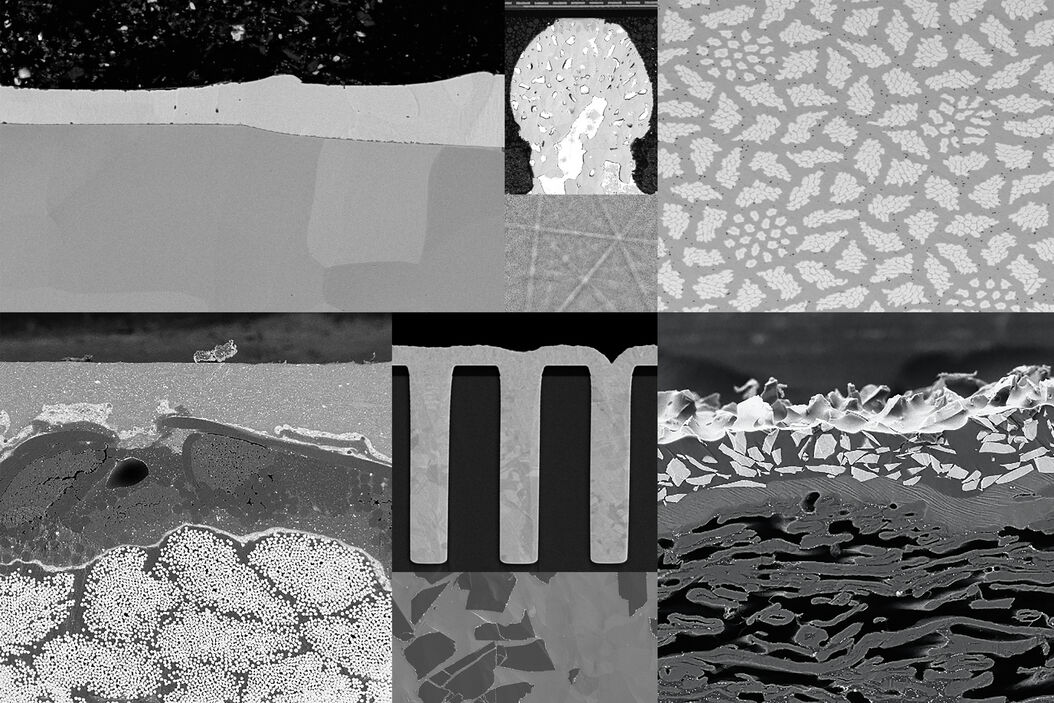
In this article you can learn how to optimize the preparation quality of your samples by using the ion beam etching method with the EM TIC 3X ion beam milling machine. A short introduction of the instrument explains how the flexible setup of the EM TIC 3X gives you the opportunity to prepare samples for various investigation areas. Understand the basic principles of the ion beam etching method to obtain high resolution SEM images for various applications. Get to know the technical working principles of the unique triple ion beam system of the EM TIC 3X and how it helps you to achieve high surface quality of cross section and planar sample preparation for SEM and