Microscopy Solutions for Battery Manufacturing
The use of batteries ranges from portable electronic devices to electric vehicles and energy storage. Cost-effective manufacturing of high-performance batteries, which are efficient, reliable, and safe, is crucial. For battery components, as the industry is still relatively new and developing, quality control (QC), failure analysis (FA), and R&D are all important.
Battery production has various steps, like electrode manufacturing as well as cell assembly and finishing, which require inspection and QC. Different solutions, from sample preparation to microscopic visual and chemical analysis, are needed during QC, FA, and R&D.
Please contact us for expert advice on our microscopy solutions for Battery Manufacturing
How are battery electrodes made?
First, raw materials for the anode and cathode are mixed to produce a homogeneous emulsion. Then this slurry is used to coat metal foils, normally Cu or Al, and subsequently dried. The desired electrode thickness is attained with calendering. Afterwards, the mother rolls are cut into smaller coils (daughter rolls). Finally, vacuum drying removes any residual solvent.
What is battery cell assembly?
For cell assembly, the single components, i.e., anode, cathode, and separator, are stacked or winded, depending on the cell geometry. Then, electrical contacts are made between the electrodes and terminals. Afterwards, the stack or “jelly roll” (winding) is inserted into the cell housing.
What is the cell finishing process?
The cell is filled with an electrolyte. Then gas that is generated during a pre-charging process must be removed before the cell is closed. Finally, the cell goes through an automated formation and aging process to obtain optimal battery performance.

What are the steps in battery production?
State-of-the-art battery production includes 3 main steps:
- Electrode manufacturing: Preparation of electrodes where a conductive additive and binder are mixed, then the electrode foils are coated with it, compressed during calendaring, cut to the right size (slitting), and finally dried to remove residual moisture.
- Cell assembly: Where the anode and cathode are shaped according to cell design, e.g., cylindrical, prismatic, or pouch (separation), then stacked or winded, welded, and inserted into a housing which is filled with an electrolyte.
- Cell finishing: Electrochemical activation with charging and discharging cycles (formation) to ensure operation performance and stability, followed by degassing, aging, and final testing.
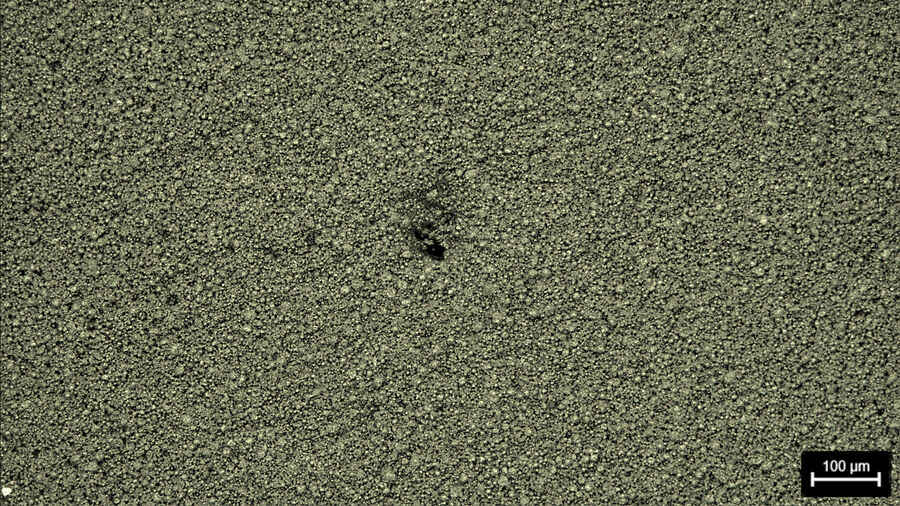
Find the Right Battery Manufacturing Solution for You!
Dedicated configurations are available for your specific needs. Answer the short questionnaire to find the right solution for your needs. If you would rather have a representative contact you, then please click here to fill out your contact information.
Contact us{{ question.questionText }}
Please select an answer!
Best Match
{{ resultProduct.header }}
{{ resultProduct.subheader }}
{{ resultProduct.description }}
{{ resultProduct.features }}
Request Your Information Package
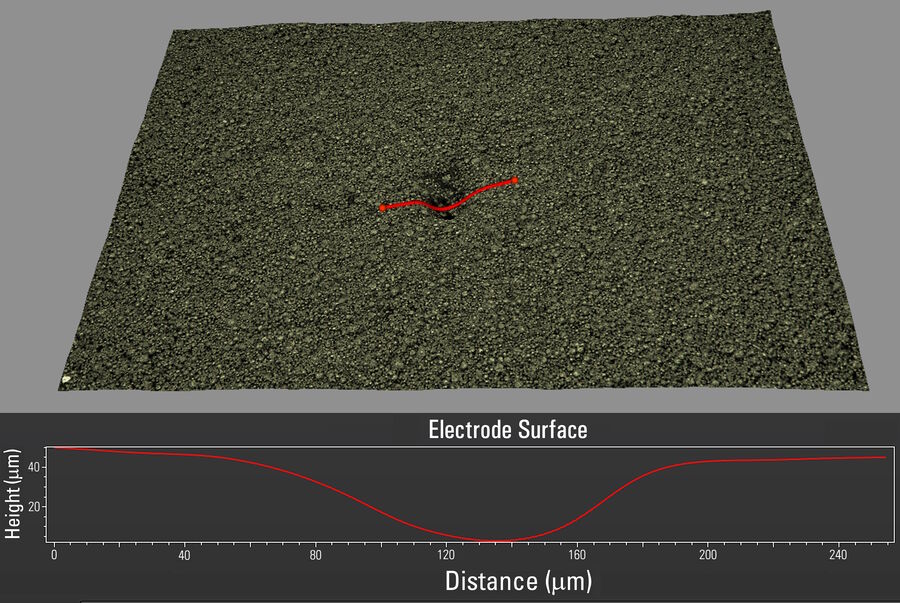
Battery electrode inspection
Electrodes are part of the smallest unit in a battery and any critical defects, e.g., impurities, blow holes in the coating, and edge waviness, on them can severely reduce battery performance and reliability.
Such defects might cause short circuits and pose safety risks for users. Also, they can hinder the ability to process electrodes, due to increased fragility. Therefore, in-line quality control and inspection of electrode surfaces and bulk homogeneity during fabrication is important. Inspection microscopes are useful for routine electrode quality checks, to ramp-up the production line, and train an AI (artificial intelligence) system to detect defects.
Burr detection for batteries
Burr detection is important, because burrs produced at the edges of electrodes, during slitting and cell assembly, can damage the separator and create short circuits. Burrs can also contribute to thermal runaway, a phenomenon which happens when the temperature control of the battery during charging is faulty. Thermal runaway creates a self-sustained increase in temperature which may cause decomposition of the battery components and ultimately fire and even an explosion.
High-performance microscopes are useful for detecting burrs during assembly, with the aim of minimizing them, helping prevent battery degradation caused by thermal runaway and short circuits.
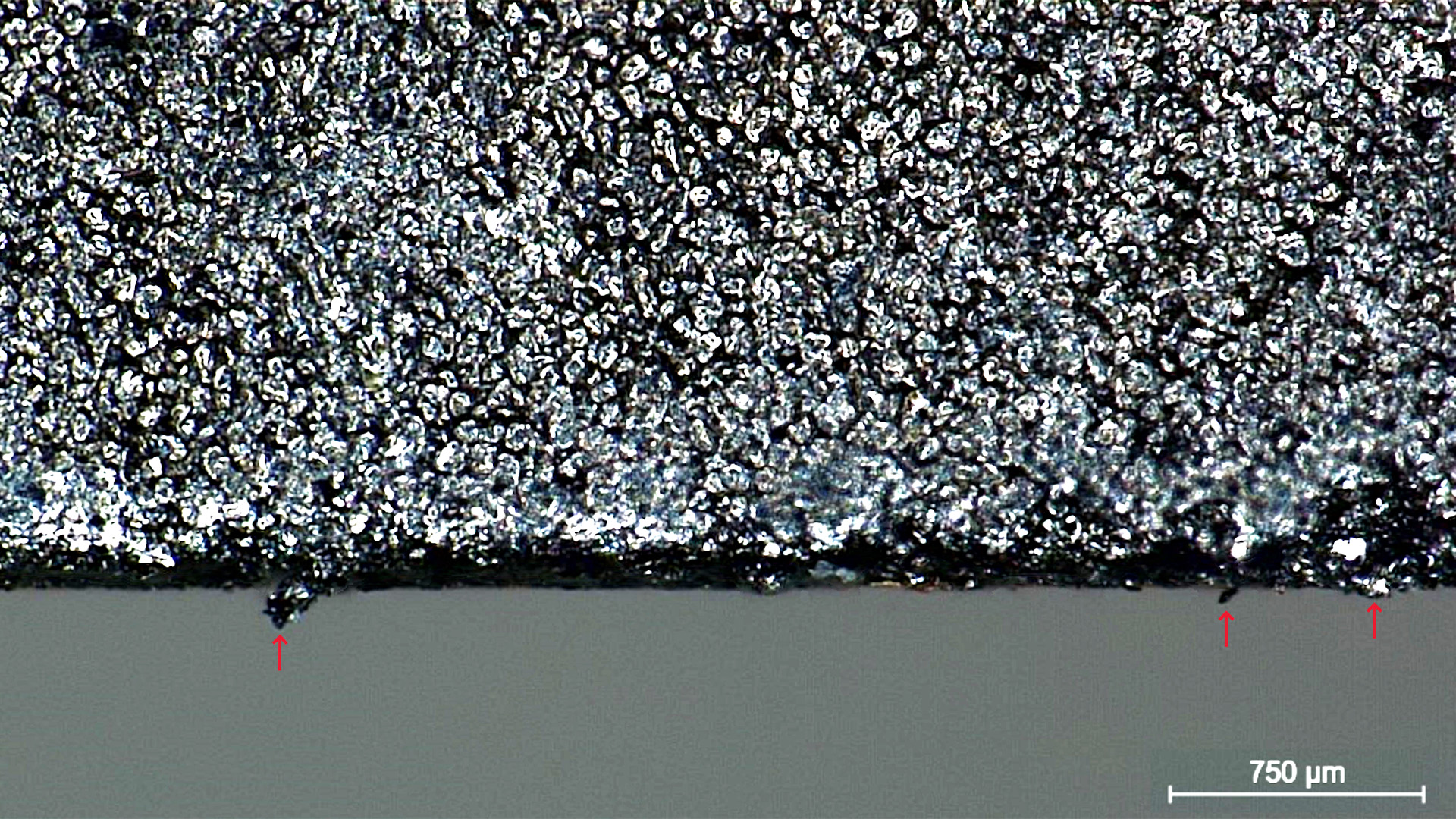
Cross-section analysis of battery components
Development and production of high-performance battery systems requires examination of component internal structures. Advanced techniques like cross-section analysis are used.
This analysis requires preparation of sample cross sections and analytical methods. Due to the brittle or soft nature of component materials, preparation can be challenging.
High-quality cross sections cannot have significant chipping (brittle materials) and smearing (soft materials). Sample handling and prep in vacuum or controlled atmospheres over several hours may be crucial. Analysis should deliver results rapidly and reliably. Solutions offering these advantages are:
- Mechanical grinding, polishing, and milling, as well as ion-beam milling systems
- Sample handling or transfer systems maintaining a vacuum or controlled atmosphere
- High-performance optical microscopes (in combination with laser spectroscopy is also possible).
Cleanliness analysis for battery production
Particle contamination during battery production can cause short circuiting and overheating which can lead to poor battery performance, short lifetimes, or even failure.
Therefore, particle detection and elimination is a critical part of quality control during components fabrication and assembly. A robust cleanliness process should be implemented for an efficient quality control during battery production.
A fast and accurate solution for cleanliness analysis is possible with optical microscopy. To have both visual and chemical evaluation, then microscopy with spectroscopy is needed.
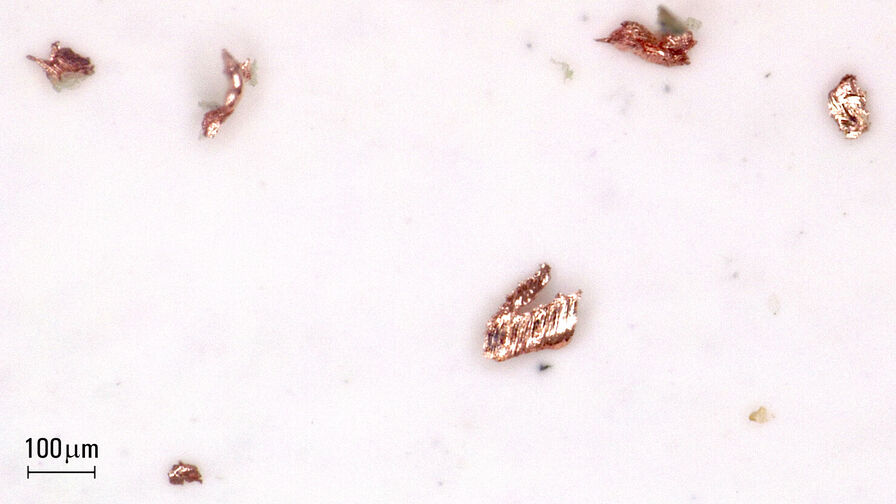